
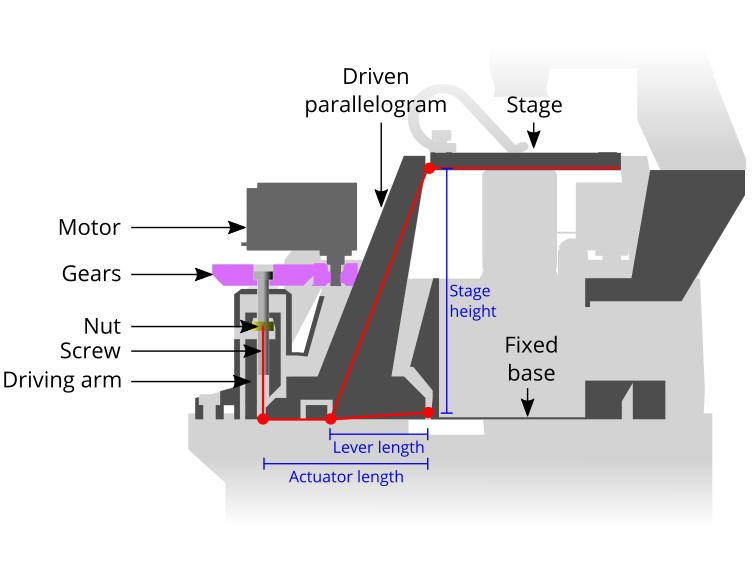
Using a Web of Things approach has resulted in a user-friendly and extremely versatile software control solution for the OpenFlexure Microscope, and we believe this approach could be generalized in the future to make automated experiments involving several instruments much easier to implement.
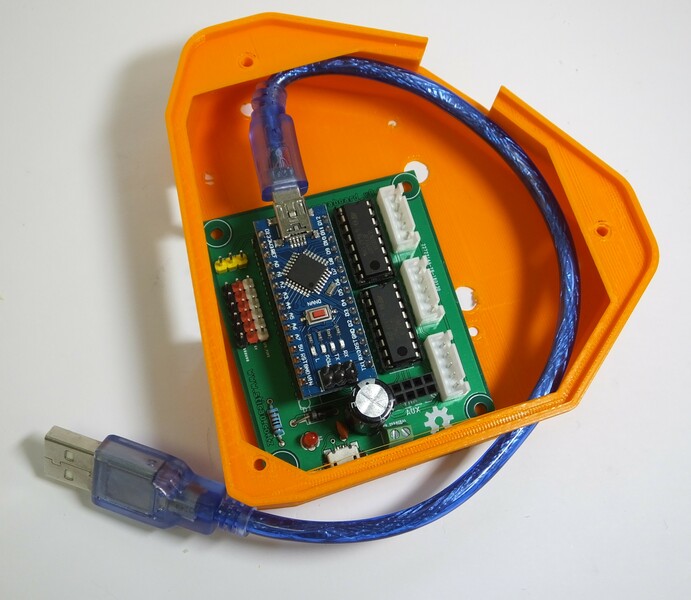
We have included an extension mechanism to add functionality, for example controlling additional hardware components or adding automation routines. Graphical and script-based clients can run simultaneously, making it easier to monitor ongoing experiments. Network control makes the software stack more robust, allows multiple microscopes to be controlled by one computer, and facilitates sharing of equipment. You no longer need to connect the microscope to a display or peripherals if you’re using the microscope from. After rebooting, the OpenFlexure Microscope Server should run automatically. When the Pi first boots, you will be asked to complete a quick setup, before rebooting. There are two standard ways to build it, with either transmission illumination or reflection illumination. Connect your Pi to a display, mouse, keyboard, and power. As the optics do not move it is particularly suited to more complex imaging (phase, reflection, fluorescence microscopy). We are interested in how distributed manufacturing of open source science hardware can work as a business model. This hardware is completely open source, you can build your own, or even sell the microscope in your location. OpenFlexure Delta Stage A 3D-printed delta-geometry stage, suitable for motorised microscopy with maximum stability. OpenFlexure Industries manufactures the OpenFlexure Microscope and OpenFlexure Block Stage. Automated control is possible from Python and Matlab, or any language that supports HTTP requests. The delta stage is a 3D printed x-y-z translation stage. An open-source, 3D-printed microscope, including a precise mechanical stage to move the sample and focus the optics.

A graphical interface is viewed either in a web browser or in our cross-platform Electron application, and gives basic interactive control including common operations such as Z stack acquisition and tiled scanning. It is the standard surgical treatment for.
#OPEN FLEXTURE CODE#
We split the control code into client and server applications interfaced via a web API conforming to the W3C Web of Things standard. Open right hemicolectomy (open right colectomy) is a procedure that involves removing the cecum, the ascending colon, the hepatic flexure (where the ascending colon joins the transverse colon), the first one-third of the transverse colon, and part of the terminal ileum, along with fat and lymph nodes. It is described in the Optics Express article.Before you start building the microscope you will need to source all the components listed in the bill of materials.Full source code for the STL files and instructions is available on GitLab. Our diverse community of users needs both graphical and script-based interfaces. The OpenFlexure Block Stage is a 3D printed x-y-z translation stage.
#OPEN FLEXTURE FULL#
We present the OpenFlexure Microscope software stack which provides computer control of our open source motorised microscope. The First Attempt Going Full Scatmos Videos.
